مقدمه: فروسیلیکو منگنز یکی از فروآلیاژهای مهم است که در صنایع فولادسازی بهخصوص برای تولید فولادهای با استحکام بالا استفاده میشود. این ماده بهدلیل دارا بودن درصد بالایی از منگنز و سیلیسیم، نقش مهمی در بهبود خواص مکانیکی فولاد ایفا میکند. با این حال، یکی از چالشهای اصلی در استفاده از فروسیلیکو منگنز، بهینهسازی درصد جذب آن در فرآیند ذوب است. درصد جذب فروسیلیکو منگنز میتواند تأثیر مستقیمی بر کیفیت نهایی فولاد تولید شده و بهرهوری اقتصادی فرآیند داشته باشد.
عوامل مؤثر بر درصد جذب فروسیلیکو منگنز در فرآیند ذوب
1. ترکیب شیمیایی فروسیلیکو منگنز:
یکی از اصلیترین عواملی که بر درصد جذب فروسیلیکو منگنز تأثیر میگذارد، ترکیب شیمیایی خود فروسیلیکو منگنز است. این آلیاژ معمولاً شامل 60 تا 70 درصد منگنز و 15 تا 20 درصد سیلیسیم است. مقدار دقیق این عناصر میتواند تأثیر مستقیمی بر روی میزان جذب آنها در مذاب فولاد داشته باشد. فروسیلیکو منگنزی که درصد بالاتری از منگنز داشته باشد، بهطور معمول جذب بیشتری را در فرآیند ذوب نشان میدهد.
2. دما و شرایط ذوب:
دما یکی از عوامل کلیدی در فرآیند ذوب است که بر جذب منگنز تأثیر دارد. در دماهای بالاتر، منگنز بهراحتی در مذاب حل میشود و درصد جذب آن افزایش مییابد. علاوه بر دما، شرایط ذوب مانند زمان نگهداری فروسیلیکو منگنز در مذاب نیز اهمیت دارد. مدت زمان بیشتری که فروسیلیکو منگنز در دمای بالا نگهداری شود، منجر به افزایش انحلال منگنز و در نتیجه جذب بیشتر آن میشود.
3. روش اضافه کردن فروسیلیکو منگنز:
نحوه افزودن فروسیلیکو منگنز به مذاب نیز نقش مهمی در جذب آن ایفا میکند. افزودن تدریجی و کنترل شده فروسیلیکو منگنز به مذاب میتواند منجر به افزایش درصد جذب شود. همچنین، زمان مناسب برای افزودن این ماده به مذاب بسیار مهم است. اگر فروسیلیکو منگنز در زمان مناسب و در دمای بهینه اضافه شود، بهطور مؤثری جذب خواهد شد.
4. شرایط احیاء و اکسیداسیون: احیاء و اکسیداسیون از دیگر عواملی هستند که میتوانند بر جذب فروسیلیکو منگنز تأثیر بگذارند. در فرآیند ذوب، حضور اکسیژن میتواند منجر به اکسیداسیون منگنز شود که در نتیجه باعث کاهش جذب آن در مذاب میشود. برای بهینهسازی جذب، باید شرایط احیاء بهگونهای کنترل شود که اکسیژن موجود در مذاب به حداقل برسد. این کار میتواند با استفاده از گازهای محافظ مانند آرگون انجام شود.
5. میزان و نوع سرباره: سرباره و ترکیب شیمیایی آن نیز بر درصد جذب فروسیلیکو منگنز تأثیر میگذارد. سربارههایی که حاوی سیلیسیم بالا هستند، میتوانند جذب منگنز را کاهش دهند. بنابراین، کنترل ترکیب سرباره و کاهش میزان سیلیسیم آن میتواند به بهبود جذب منگنز کمک کند. همچنین، باید دقت کرد که سرباره به درستی از مذاب جدا شود تا از کاهش درصد جذب جلوگیری شود.
6. سرعت سرد شدن مذاب: سرعت سرد شدن مذاب یکی دیگر از عواملی است که بر جذب فروسیلیکو منگنز تأثیر میگذارد. زمانی که مذاب به آرامی سرد میشود، زمان بیشتری برای جذب منگنز فراهم میشود. این امر بهویژه در فرآیندهای تولید فولاد با خواص مکانیکی بالا مهم است. سرعت سرد شدن کمتر، باعث میشود که منگنز بهطور یکنواخت در ساختار فولاد توزیع شود و از تشکیل نواحی ضعیف جلوگیری کند.
7. نوع کوره و تکنولوژی ذوب: نوع کوره مورد استفاده در فرآیند ذوب، مانند کورههای القایی یا قوس الکتریکی، نقش مهمی در جذب فروسیلیکو منگنز دارد. کورههای قوس الکتریکی به دلیل دمای بالا و شرایط کنترل شده، معمولاً جذب بهتری از منگنز را فراهم میکنند. در حالی که در کورههای القایی، ممکن است به دلیل دمای کمتر و زمان کوتاهتر ذوب، درصد جذب کاهش یابد. انتخاب کوره مناسب و تنظیم پارامترهای فرآیند بر اساس نیازهای تولید میتواند به بهبود جذب فروسیلیکو منگنز کمک کند.
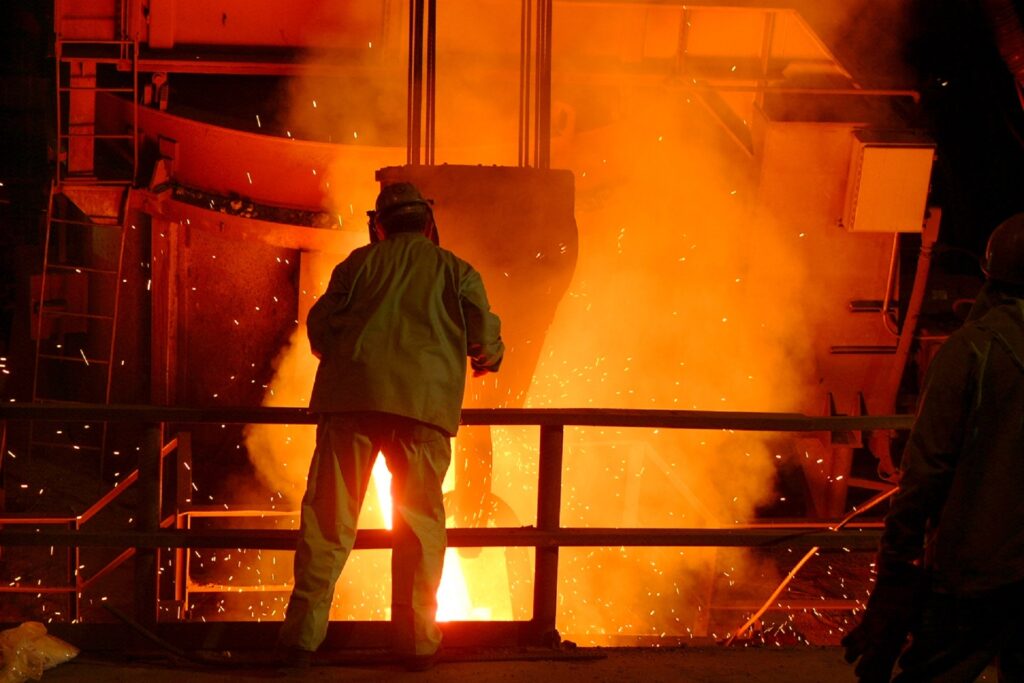
تجربیات عملی و نکات نهایی: بر اساس تجربیات من در همکاری با کارخانههای فولادسازی با تکنولوژیهای مختلف مانند کورههای القایی و قوس الکتریکی، بهینهسازی شرایط جذب فروسیلیکو منگنز نیازمند یک رویکرد جامع و دقیق است. خرید مستقیم از تولیدکنندگان معتبر فروسیلیکو منگنز در ایران، نظارت دقیق بر فرآیند بارگیری و تحویل از کارخانه، و استفاده از روشهای کنترل کیفیت مؤثر مانند آزمایشهای مکرر از هر محموله، میتواند به اطمینان از کیفیت و درصد جذب مطلوب این ماده کمک کند.
جمعبندی: در نهایت، جذب فروسیلیکو منگنز در ذوب به مجموعهای از عوامل فنی و شرایط عملیاتی بستگی دارد که باید بهدقت مدیریت شوند. انتخاب صحیح فروسیلیکو منگنز با ترکیب شیمیایی مناسب، کنترل دقیق شرایط ذوب، بهینهسازی روشهای افزودن و سرد کردن مذاب، و استفاده از تکنولوژیهای مناسب، همگی میتوانند به افزایش درصد جذب و در نتیجه بهبود کیفیت نهایی فولاد تولید شده کمک کنند. برای کسب اطلاعات بیشتر و مشاوره تخصصی در این زمینه، با ما در تماس باشید تا بتوانیم بهترین راهحلها را برای نیازهای تولیدی شما ارائه دهیم.